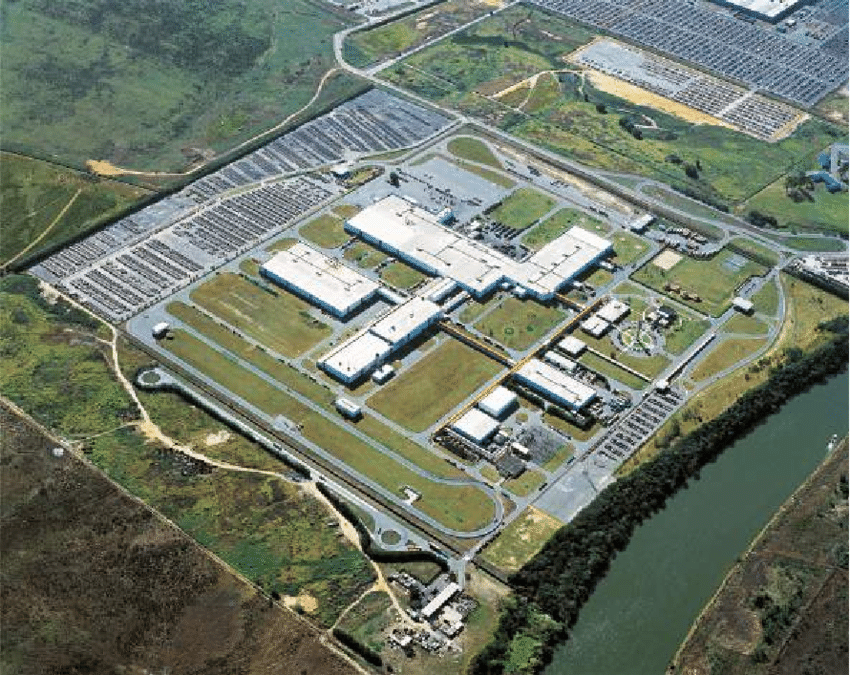
Con inversiones de R$ 500 millones, el complejo de desarrollo y producción Volkswagen Caminhões e Ônibus en Resende (RJ) experimentó una verdadera revolución para albergar una de las líneas de camiones más modernas de América Latina, dedicada exclusivamente a los nuevos extrapesados Volkswagen.
Desde el chasis hasta el acabado de la cabina, todo el proceso fue creado de acuerdo con los conceptos de fabricación 4.0, con robótica avanzada e inteligencia Big Data para una mayor productividad y seguridad en la operación. Ahora la fábrica de VW Caminhões e Ônibus en Resende cuenta con más de 70 robots, un tercio de los cuales están dedicados a la línea Meteor, además de un sistema de datos 100% en la nube para construir la nueva cabina.
Los recursos se invirtieron en la instalación de un nuevo proceso para enmarcar la cabina, con un 80% de automatización, y también en la construcción de un edificio de cerca de 4,5 mil metros cuadrados dedicados al acabado del camión con el montaje de más de mil piezas del interior de la cabina.
La inversión también incluye una nueva área de logística para asegurar una mayor eficiencia en el suministro e inventario de componentes. Los equipos más modernos también se convierten en parte de la línea de ensamblaje final para aumentar la eficiencia y la productividad.
Cabinas con chips – Dentro del concepto Big Data, la cabina recibe un chip que permite su identificación durante todo el proceso de fabricación. Así es posible programar los robots de forma remota y también conocer el estado del vehículo desde cualquier parte del mundo. Esta información almacenada en la nube permite el monitoreo en tiempo real por parte del equipo de especialistas de VWCO, con el fin de utilizar la información para alinear toda la estrategia de producción y ventas.
Este chip se instala justo al inicio del montaje, aún en la línea de armazón, que ocupa una superficie de 2,8 mil metros cuadrados y alberga más de 130 nuevos equipos, responsables de un proceso de soldadura que es 100% automatizado por primera vez en VWCO, alcanzando 2.846 puntos de soldadura. El análisis de calidad final también sigue la misma línea, con cámaras que se encargan de toda la medición para garantizar la perfección de la cabina. Los robots también se encargan de la aplicación de pegamento, la fijación de clavijas y el transporte de placas metálicas.
Vehículos guiados automáticamente sin precedentes: en el nuevo edificio de acabado de la cabina, más innovaciones, en sintonía con lo más moderno de Europa. Por primera vez, VWCO emplea vehículos guiados automáticamente (los llamados AGV) para transportar el vehículo en su línea de montaje. Esto aporta mucha flexibilidad al modelo de producción de la montadora, lo que permite adaptaciones rápidas y optimiza los recursos.
Los AGV navegan por inducción utilizando frecuencias incrustadas en el piso del edificio. Hay todo un sistema inteligente para hacer su operación más eficiente: un escáner de seguimiento para evitar colisiones y una estación de carga automática para tus baterías también instalada en el piso.
El movimiento de toda la línea se realiza de forma automática, controlado por el sistema Big Data. La información del proceso está disponible en pantallas a lo largo de toda la línea, en cada una de las 15 estaciones de montaje. Esta hiperconectividad controla cada etapa e impide, por ejemplo, el movimiento de cualquier vehículo sin la seguridad necesaria o que la actividad se haya completado. La lectura inteligente se realiza mediante sensores instalados en el edificio.
Paralelamente al acabado de la cabina, existen líneas de premontaje de sus puertas, tablero de instrumentos y techo, secuenciadas al cronograma de producción. El eficiente sistema de automatización también optimiza el uso del mismo robot que aplica cola de techo, tablero de instrumentos, parabrisas y ventanilla. Otra novedad es la adopción de un solo pegamento para las cuatro aplicaciones, reduciendo costos y desperdicio al medio ambiente.